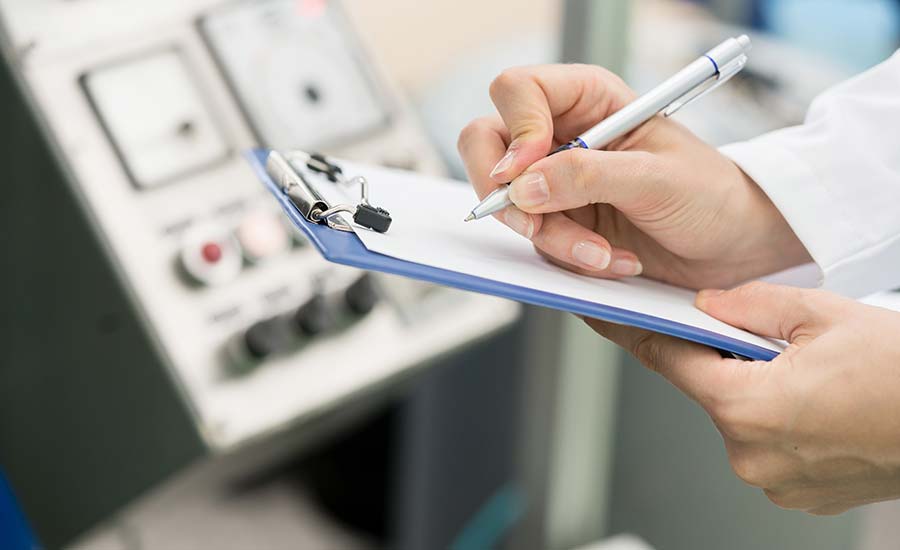
In industries where even the smallest errors can cause catastrophic failures or product recalls, quality control and assurance are essential processes.
The difference between quality control (QC) and quality assurance (QA) is more than just the terminology.
QC checks that every final product meets industry standards, while QA implements and develops protocols that prevent errors from happening at all.
Today, we’ll cover what QC and QA are, discuss the main differences between the two, and explain best practices for both processes.
What Is Quality Control (QC) and Quality Assurance (QA)?
Both quality control and assurance are often confused as the same process, but they serve completely different purposes in manufacturing and supply chain operations.
Quality Control Definition
Quality control (QC) is a product-focused process that ensures every component meets predefined quality standards before reaching the customer. It involves inspection, testing, and defect detection to eliminate faulty components before they are integrated into final assemblies.
QC measures include:
- Visual and functional inspections: These consist of inspecting physical defects, inconsistencies, or damage in components.
- Advanced testing procedures: With the use of X-ray analysis, digital microscopy, and functional testing, these tests are done to verify authenticity and performance.
- Batch sampling and statistical analysis: To check the consistency of a certain product, random samples are taken from production to ensure quality.
Example: In electronics manufacturing, a QC team tests microprocessors for defects before they are installed in high-performance computing systems.
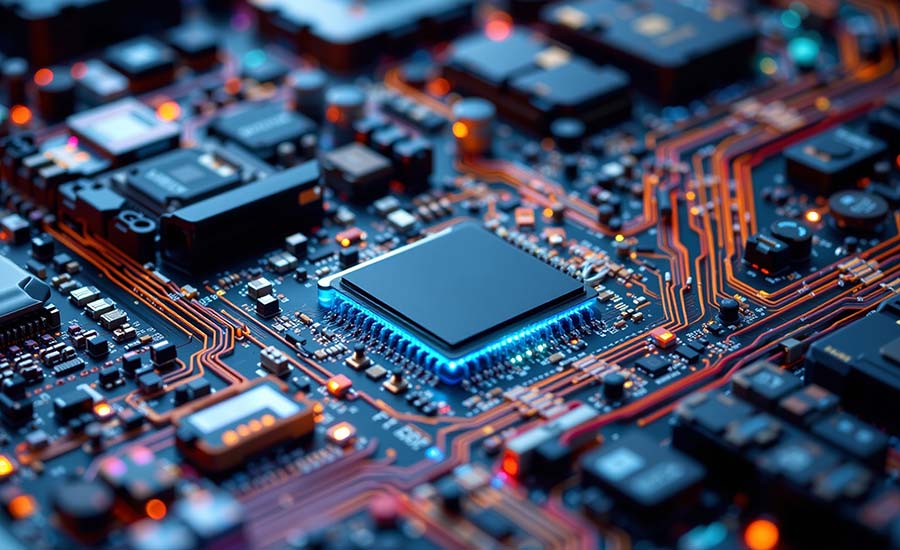
Quality Assurance Definition
Quality assurance (QA) is a process-driven approach that prevents defects before they happen.
QA teams don’t inspect final products, they make sure the whole process is integrated in the manufacturing and supply chain from the start.
QA measures include:
- Supplier audits and compliance checks: This measure is taken to guarantee that all source components meet necessary quality and industry standards.
- Standardized operating procedures (SOPs): This is done to establish strict protocols for handling, storing, and assembling electronic components.
- Continuous improvement initiatives: Since QA is not a static process, using feedback to improve the manufacturing workflow is extremely important.
Key Differences Between Quality Control and Quality Assurance
While quality control (QC) and quality assurance (QA) work together, they serve different purposes in maintaining high product standards.
1. Purpose and Focus
The main difference between QC and QA lies in what they prioritize:
- QC focuses on detecting and correcting defects in individual components before they are distributed or assembled.
- QA focuses on building systems and processes that prevent defects from occurring in the first place.
Example: Let’s take a manufacturer that produces high-performance microprocessors for industrial automation. QC would inspect finished microprocessors for defects, while QA would ensure the entire production process follows strict standards to reduce the risk of faulty units being produced in the first place.
2. Process vs. Product Approach
Quality control is a product-focused process, while quality assurance is a process-focused approach.
- QC measures the quality of a final product through inspections, testing, and analysis.
- QA develops systems and workflows that improve manufacturing consistency, material handling, and supplier compliance.
Example: In electronic component sourcing, QC would involve testing capacitors and microcontrollers for failure rates, while QA would audit suppliers, enforce sourcing protocols, and set industry-aligned standards for procurement.
Reactive vs. Proactive Methods
Another key difference is when QC and QA teams operate:
- QC is reactive when it identifies issues after production and prevents defective parts from reaching customers.
- QA is proactive when it establishes preventative measures and protocols to avoid quality issues before production begins.
Example: In medical electronics manufacturing, QA checks that only certified, high-quality components are sourced for life-saving devices like pacemakers. If a problem does happen, QC steps in to test and isolate defective units before shipment, preventing faulty medical devices from entering the market.
The Role of QC vs. QA in Electronics Manufacturing
A single defective component can lead to system failures, costly recalls, or even safety risks, especially in aerospace, medical, and industrial applications.
Ensuring Compliance With Industry Standards
Electronics manufacturers must meet strict international regulations to ensure product safety, durability, and efficiency.
QA and QC must maintain compliance with:
- ISO 9001: Global quality management standards for manufacturing
- AS9100: Aerospace industry requirements for safety and performance
- ISO 13485: Medical device manufacturing regulations
- IPC Standards: Industry guidelines for electronic assemblies and PCB manufacturing
Example: A medical device manufacturer must follow ISO 13485 to ensure that components used in pacemakers or MRI machines meet strict safety and performance criteria. QA ensures that only certified components enter production, while QC tests each batch for precision and functionality before distribution.
Preventing Defective Components in Production
QC and QA help eliminate defective parts before they reach end products, preventing:
- Power failures due to faulty capacitors
- Signal distortion caused by substandard resistors
- Short circuits from improperly manufactured semiconductors
Example: A manufacturer producing high-speed processors for aerospace applications cannot afford even minor defects. QA ensures that sourcing and handling protocols meet military-grade standards, while QC identifies and isolates defective chips before assembly, ensuring flawless functionality in extreme environments.
Improving Supply Chain Reliability
A strong supply chain depends on consistently high-quality components.
QA and QC work together to:
- Vet suppliers for compliance with global standards
- Prevent counterfeit or low-grade components from entering production
- Reduce delays and failures caused by sourcing inconsistencies
Example: During the global chip shortage, companies that prioritized QA in supplier selection were able to secure reliable semiconductor sources, ensuring continuous production. Meanwhile, QC teams verified incoming shipments to prevent counterfeit or low-quality parts from disrupting manufacturing.
Best Practices for Implementing Quality Control and Quality Assurance
To ensure high-performance, defect-free electronic components, manufacturers must integrate both quality control (QC) and quality assurance (QA) best practices into their processes.
When integrating both processes, you should:
- Establish a thorough inspection process: Multi-layer inspections at different production stages help catch defects early.
- Utilize advanced testing and automation: Automated optical inspection (AOI) detects defects faster and with higher accuracy than manual checks.
- Implement continuous monitoring and process improvements: Tracking key quality metrics like defect rates and rework percentages helps identify trends. A feedback loop between QC and production teams resolves recurring issues, while regular training ensures engineers and technicians stay updated on the latest QA/QC methodologies.
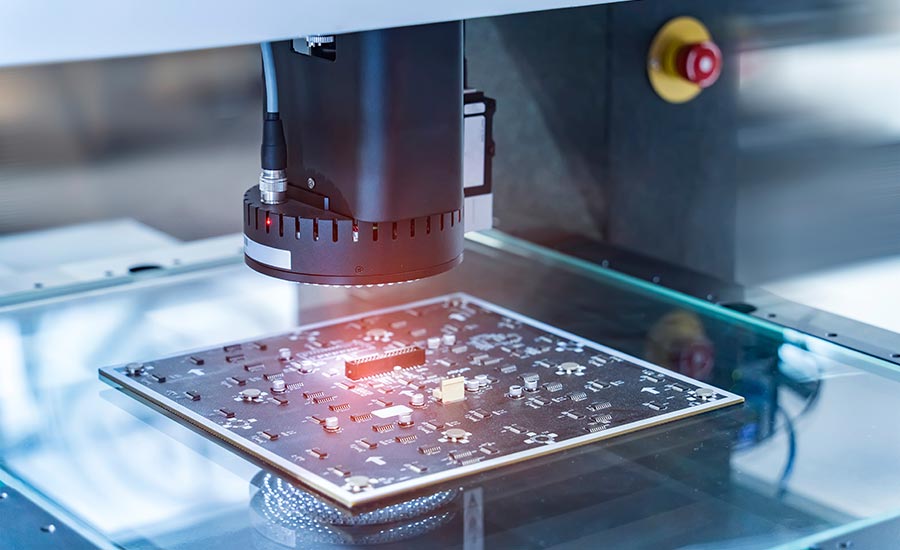
How AGS Devices Maintains the Highest Quality Standards
At AGS Devices, quality control and assurance aren’t just regular checkmarks in our notebooks — they’re a golden standard.
To ensure we meet the highest standards, product inspections begin as soon as materials arrive at our facility.
Here’s why no one doubts our quality processes:
- Industry-leading certifications: We comply with ISO 9001, AS9120, and IDEA-STD-1010-B to guarantee strict quality management and counterfeit prevention.
- Advanced testing and inspection: Our QC process includes X-ray analysis, digital microscopy, functional testing, and batch sampling to eliminate defective or counterfeit parts.
- Trusted supplier network: We rigorously vet and audit our suppliers to ensure every component comes from verified and reliable sources.
- Strict compliance standards: Every product we distribute aligns with global manufacturing and safety standards, ensuring full traceability and authenticity.
- Customer-first approach: We work closely with our clients, offering custom quality assurance solutions to meet the specific demands of industries like aerospace, medical, and industrial electronics.
By combining cutting-edge testing, strong supplier relationships, and strict compliance measures, AGS Devices delivers electronic components that meet the highest standards of quality and reliability—helping manufacturers reduce risk, prevent failures, and maintain a resilient supply chain.