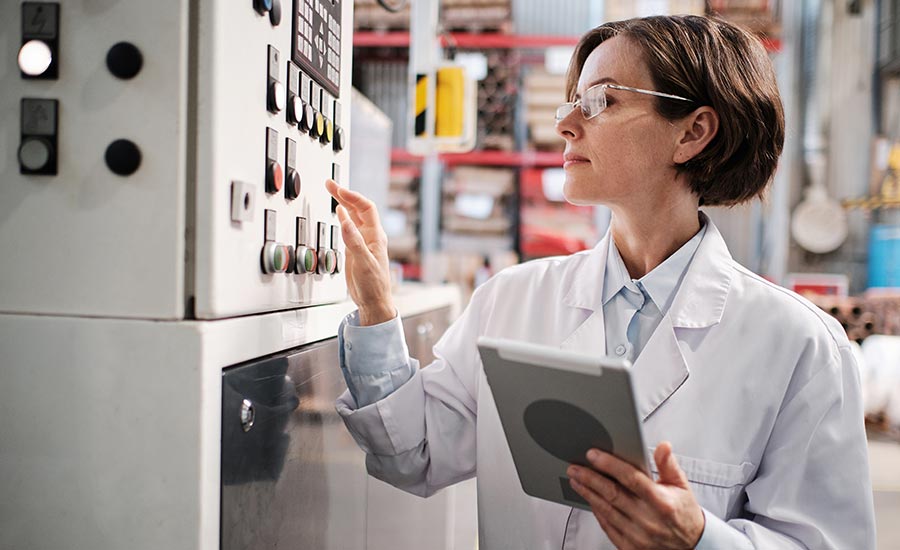
A manufacturing bill of materials (MBOM) serves as a foundational blueprint, detailing every component, subassembly, and process required to transform raw materials into a finished product.
This documentation is not just a formality, it’s a tool for efficient production, cost control, and quality assurance.
A well-structured MBOM can yield substantial time savings by ensuring all necessary components are accounted for and readily available, streamlining the manufacturing process.
In this blog, we’re going to cover what an MBOM is, its key components, the benefits of using it, and how it’s used in manufacturing.
What Is a Manufacturing BOM (MBOM)?
A manufacturing bill of materials (MBOM) is an important document that bridges the gap between product design and production.
It provides a detailed, structured list of all components, subassemblies, raw materials, and processes required to manufacture a product.
Unlike an engineering BOM (EBOM), which focuses on the design specifications, an MBOM is production-centric, ensuring every element needed for assembly is accounted for.
Key Elements of an MBOM
An MBOM includes:
- Components and subassemblies: A comprehensive list of parts, including quantities, part numbers, and descriptions.
- Manufacturing instructions: Details about assembly processes, including tools and equipment required.
- Process dependencies: Information on sequencing, timing, and interdependencies between various stages of production.
Key Components of an MBOM
A MBOM is much more than a simple list of parts — it’s a document that serves as a roadmap for turning raw materials into finished products.
Key components of MBOM include:
Detailed Component Information
At the heart of every MBOM is a complete inventory of components required for manufacturing.
Detailed component information includes:
- Part numbers and descriptions: Every item is uniquely identified with part numbers and clear descriptions, providing precise procurement and assembly.
- Quantities and specifications: Accurate quantity data prevents shortages and overstocking, while detailed specifications provide compatibility with design requirements.
- Subassemblies: Complex products often require pre-assembled modules, and the MBOM includes details on how these subassemblies integrate into the final product.
For example, in electronics manufacturing, an MBOM might list resistors, capacitors, and PCBs with their specific technical attributes, so each component meets the design’s performance needs.
Production Process Details
An MBOM also provides critical insights into the manufacturing process, detailing how components come together to form the finished product.
The production process includes:
- Assembly instructions: Step-by-step guidance on how to combine components, including specific tools and techniques required.
- Sequencing and dependencies: Information on the order in which components should be assembled for efficiency and minimizing errors.
- Quality control steps: Highlighting key checkpoints during assembly to maintain consistency and adherence to industry standards.
For example, in PCB assembly, the MBOM would include soldering requirements, testing protocols, and precise positioning of components to provide functionality and reliability.
Supporting Documentation
A well-structured MBOM links directly to critical supporting documents that enhance clarity and compliance.
Supporting documentation includes:
- CAD drawings: Detailed diagrams that visually represent the product and its components.
- Compliance certificates: Documentation that verifies materials meet regulatory standards, such as RoHS or REACH for electronic components.
- Testing and validation data: Reports on prior testing results, so components and processes meet performance expectations.
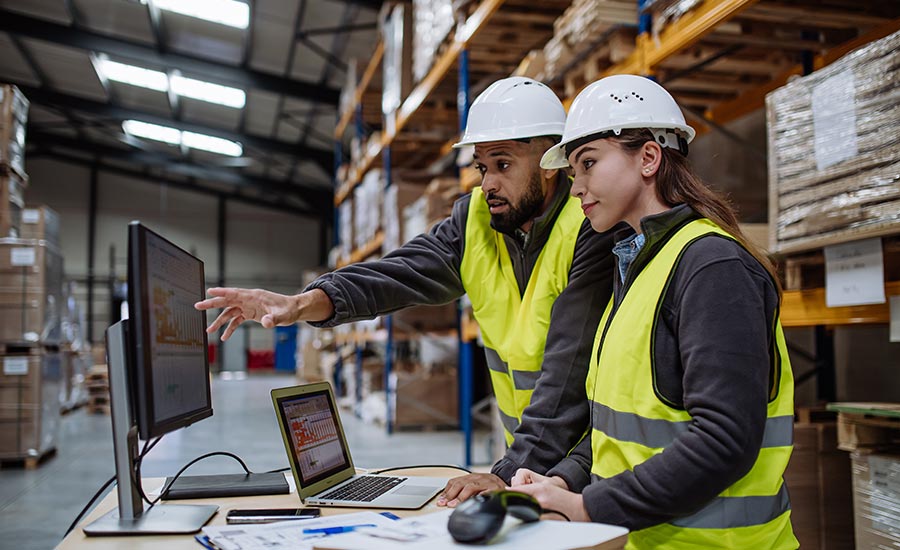
The Role of MBOM in Manufacturing
By providing a comprehensive framework for production, an MBOM secures that every step of the manufacturing process is optimized for success.
The role of MBOM in manufacturing is to:
1. Improve Production Processes
An MBOM simplifies and organizes production workflow by aligning all necessary components, tools, and instructions.
- Efficient resource allocation: By detailing the exact quantities and specifications of materials needed, an MBOM guarantees resources are allocated precisely, avoiding overstocking or shortages.
- Easy assembly: Step-by-step assembly instructions and process dependencies help manufacturing teams execute tasks efficiently and without delays.
- Optimized scheduling: With clear insights into the sequence of operations, production managers can schedule tasks to minimize downtime and maximize throughput.
For example, in electronics manufacturing, an MBOM enables smooth assembly of intricate devices like smartphones by ensuring every component is available and processes are synchronized.
2. Reduce Errors and Waste
Errors and waste in manufacturing can lead to significant cost overruns and project delays. An MBOM helps mitigate these risks by providing clarity and control.
- Minimizing rework: By specifying exact tolerances and material requirements, an MBOM reduces the chances of errors during assembly.
- Preventing overproduction: Accurate component data helps prevent the overuse of materials, aligning production output with demand.
- Improving quality assurance: Integrated quality control steps within the MBOM ensure every stage of production meets design and performance standards.
For example, in the assembly of printed circuit boards (PCBs), an MBOM secures that only approved components are used, reducing the risk of faulty products and wasteful rework.
3. Enhance Collaboration Across Teams
An MBOM acts as a central reference point, aligning different departments and stakeholders involved in the manufacturing process.
Design and manufacturing alignment: By translating design specifications into actionable production details, the MBOM bridges the gap between engineering and manufacturing teams.
Improved supplier coordination: Procurement teams can use the MBOM to source the exact materials needed, providing timely delivery and cost efficiency.
Cross-department transparency: With access to the same detailed information, teams can work cohesively, minimizing miscommunication and delays.
For example, in automotive manufacturing, the MBOM helps engineers, suppliers, and assembly teams collaborate easily to produce high-performance vehicles with precision.
Benefits of a Well-Structured MBOM
A well-structured MBOM is a foundation of successful manufacturing.
Some benefits of a well-structured MBOM include:
1. Precise Production Efficiency
One of the most significant benefits of a well-structured MBOM is its ability to improve manufacturing operations.
It makes sure that every component, tool, and resource needed for production is available when required, reducing delays and minimizing downtime.
Clear assembly instructions and process sequencing enable manufacturing teams to work with precision, eliminating guesswork and improving overall productivity.
For example, in the assembly of electronic devices, like circuit boards, an MBOM can ensure each part is installed in the correct order, resulting in faster and more efficient production cycles.
2. Profitable Cost Management
Accurate and detailed MBOMs play a vital role in controlling manufacturing costs. By specifying exact quantities of materials, an MBOM prevents overstocking, reducing inventory carrying costs.
Because of MBOMs, procurement teams source only the necessary components, eliminating wasteful spending.
Additionally, by aligning production with demand, the MBOM helps manufacturers avoid overproduction and the associated financial losses.
In industries like automotive manufacturing, this precision contributes to maintaining profitability while meeting stringent budget constraints.
3. Risk-Free Quality Assurance
Quality is at the heart of any successful manufacturing operation, and a well-structured MBOM provides consistency and reliability in the final product.
By incorporating quality control checkpoints and compliance requirements, the MBOM minimizes variability and makes sure that every unit meets design specifications.
This is particularly important in sectors like healthcare and aerospace, where the performance and safety of products are non-negotiable.
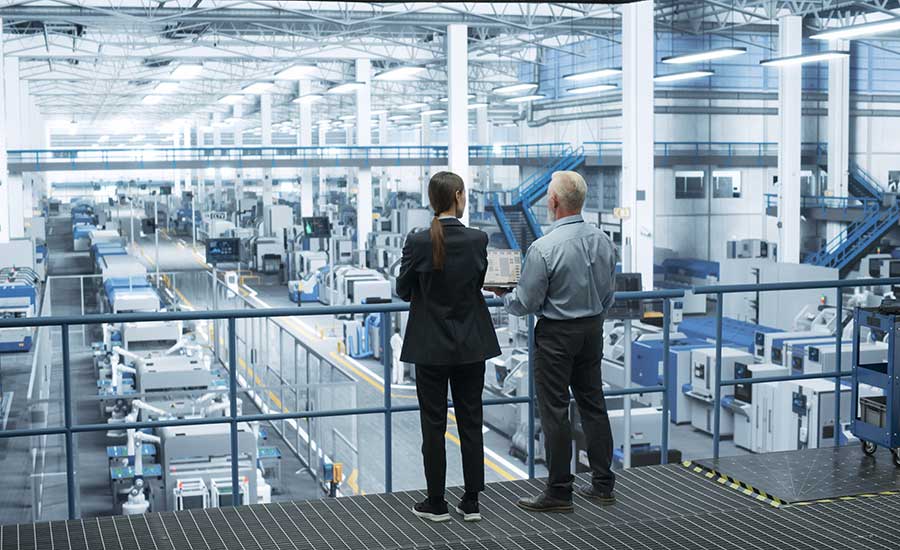
How AGS Devices Supports MBOM Optimization
At AGS Devices, we recognize the critical role a manufacturing bill of materials (MBOM) plays in yielding efficient and precise production processes.
By uploading your MBOM to our platform, we provide fast and accurate part verification against our in-stock inventory, ensuring the components you require are readily available.
In addition to optimizing your MBOM management, we offer comprehensive support services, including:
Our dedicated account representatives and sales managers work closely with you to find cost-effective and timely solutions for any supply challenges. With open and proactive communication, we make sure you’re always informed about changes that could impact your production timeline.
Start optimizing your MBOM today with AGS Devices and keep your manufacturing operations moving forward.