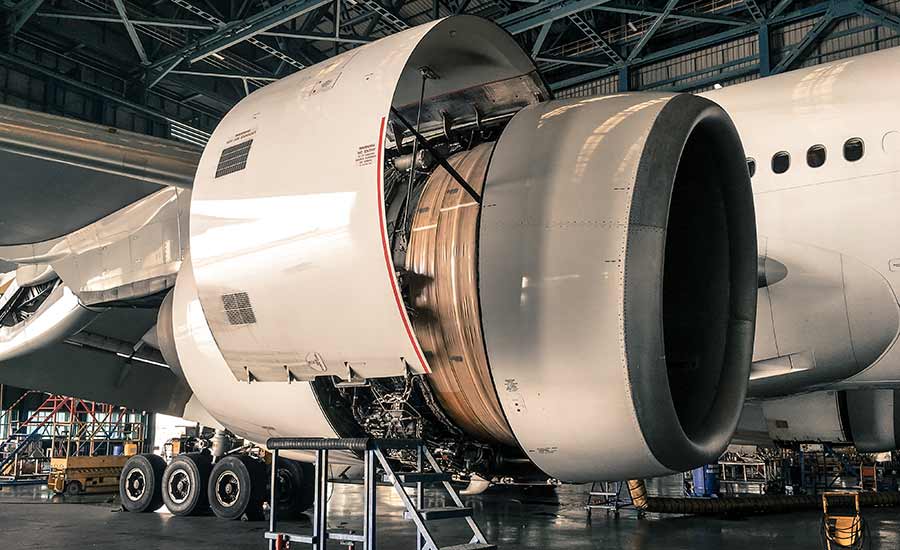
Quality control is not just a checkbox — it’s a critical lifeline for safety and reliability in aerospace manufacturing
Recent safety issues with Boeing, one of the industry’s giants, have proved that quality control is essential. The grounding of the 737 Max, following two tragic crashes that claimed 346 lives, highlighted significant lapses in Boeing’s quality assurance processes.
Robust quality control measures can reduce manufacturing costs by up to 20% and increase compliance with safety regulations by 30%.
We’ll cover recent Boeing quality control issues, cover important aspects of quality control in the aerospace industry, and explain how AGS Devices handles quality control processes.
Overview of Recent Boeing Plane Issues
Boeing, one of the world’s largest aerospace manufacturers, has faced a series of significant issues in recent years that have impacted its reputation and operations.
The key challenges include safety concerns, production flaws, and regulatory processes, which have collectively underscored the importance of quality control measures.
1. The 737 Max Crises
One of the most notable issues was the grounding of the 737 Max fleet following two tragic crashes in 2018 and 2019. Investigations revealed that faulty software, known as the Maneuvering Characteristics Augmentation System (MCAS), played a crucial role in these accidents.
This led to a global grounding of the 737 Max, lasting nearly 20 months, and prompted intense criticism of Boeing’s design and certification processes.
2. Production Flaws in the 787 Dreamliner
Boeing has also encountered significant production issues with its 787 Dreamliner. Manufacturing defects, including gaps in the fuselage and problems with the horizontal stabilizer, led to production halts and delays in deliveries.
These flaws required comprehensive inspections and repairs, further straining Boeing’s production capabilities and financial performance.
3. Quality Control Lapses
In addition to specific model-related issues, Boeing has faced broader quality control lapses across various production lines.
Reports of foreign object debris (FOD) left inside completed aircraft and concerns about supplier oversight have highlighted systemic weaknesses in Boeing’s quality assurance processes. These lapses have led to increased regulatory scrutiny and calls for more rigorous quality control standards.
The Critical Role of Quality Control in Aerospace
Quality control in aerospace electronics and industry is of paramount importance, as it directly impacts safety, compliance, and the overall trust of the flying public.
Given the complexities and high stakes associated with aviation, stringent quality control measures are essential to ensure that every component and system operates flawlessly.
The quality control in aerospace also helps with:
1. Ensuring Safety
Safety is the foremost priority in aerospace, and rigorous quality control is crucial in mitigating risks. Aircraft are made of thousands of components, each of which must perform reliably under extreme conditions.
A single flaw can lead to catastrophic failures. Therefore, comprehensive testing, meticulous inspections, and adherence to stringent manufacturing standards are necessary to identify and rectify potential issues before they result in serious incidents.
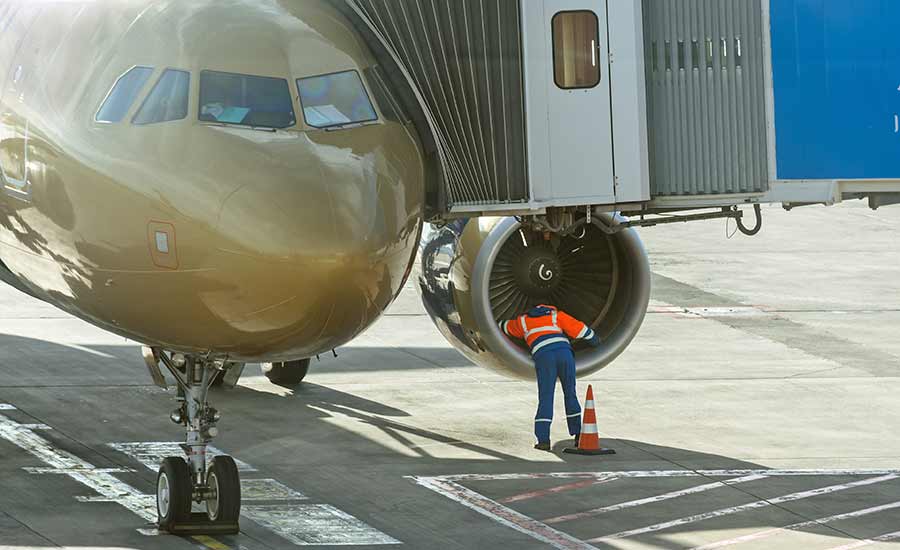
2. Regulatory Compliance
The aerospace industry is heavily regulated, with agencies like the Federal Aviation Administration (FAA) and the European Union Aviation Safety Agency (EASA) enforcing strict standards.
Quality control ensures compliance with these regulations, which cover everything from design and manufacturing to maintenance and operations. Non-compliance can result in severe penalties, grounding of fleets, and loss of certification, which can be detrimental to manufacturers and operators alike.
3. Building Trust and Reputation
Trust is an essential asset in the aerospace sector. Airlines, passengers, and regulators must have confidence in the safety and reliability of aircraft. Robust quality control processes build this trust by demonstrating a commitment to excellence and safety.
Companies that consistently deliver high-quality products maintain strong reputations and customer loyalty, while those that fail to prioritize quality control face significant reputational damage.
4. Economic Efficiency
While implementing stringent quality control measures can be resource-intensive, it ultimately leads to economic efficiency. Detecting and addressing issues early in the production process reduces the likelihood of costly recalls, repairs, and downtime.
This proactive approach not only saves money but also ensures timely delivery and operational reliability, which are crucial for maintaining competitive advantage in the aerospace industry.
Strategies for Improving Quality Control
Improving quality control in the aerospace industry is essential to prevent quality control issues that have recently plagued companies like Boeing.
Here are three key strategies for enhancing quality control:
1. Leveraging Advanced Technologies
Implementing advanced technologies can significantly enhance the quality control process in aerospace manufacturing. Utilizing AI and machine learning algorithms allows for the early detection of defects and anomalies that might be missed by human inspection.
These technologies can analyze vast amounts of data from production lines to identify patterns and predict potential failures before they occur.
Additionally, the integration of the Internet of Things (IoT) enables real-time monitoring of manufacturing processes. IoT devices can continuously collect data on various parameters such as temperature, pressure, and vibration, providing instant feedback and allowing for immediate corrective actions.
2. Strengthening Supplier Oversight
Supplier quality is crucial in aerospace manufacturing, as many components are sourced from external suppliers. Strengthening supplier oversight involves regular audits and assessments to ensure that suppliers adhere to stringent quality standards.
Establishing a robust supplier quality management system can help identify and mitigate risks associated with third-party components.
Collaborating with suppliers is also key. Working closely with suppliers to share best practices and quality expectations can lead to improved quality throughout the supply chain.
3. Enhancing Employee Training Programs
Human factors play a crucial role in maintaining high-quality standards. Enhancing employee training programs ensures that all personnel involved in the manufacturing process are well-versed in the latest quality control techniques and standards.
Continuous education and upskilling of employees can keep them updated on new technologies, processes, and regulatory requirements.
Creating a quality-centric culture within the organization is also vital. Encouraging employees to take ownership of quality and empowering them to report issues without fear of reprisal fosters an environment where quality is prioritized.
Implementing regular training sessions, workshops, and quality awareness programs can reinforce this culture and ensure that every team member understands their role in maintaining high-quality standards.
AGS Devices’ Quality Control Process
At AGS Devices, our commitment to quality control is paramount, especially given the high stakes in the aerospace industry. Ensuring the reliability and performance of electronic components is crucial in aerospace, where even the smallest defect can have significant consequences.
Our rigorous quality control process is designed to meet the stringent demands of this industry, guaranteeing that our components enhance the safety and efficiency of aerospace applications.
1. Three-Tier Quality Control System
Our quality control process begins with a meticulous three-tier system that includes incoming receiving inspection, quality authenticity testing, and outbound shipment verification.
To explain each stage in more detail:
- Incoming receiving inspection: This initial phase starts as soon as the materials arrive at AGS Devices. Our team scrutinizes all packaging, from outer cartons to individual material packaging like reels, tubes, and trays, to detect any potential damage. Documentation verification ensures that material accuracy, quantities, date codes, lot numbers, and certificates align with manufacturer specifications and customer expectations.
- Quality authenticity testing: Our state-of-the-art testing process includes mechanical testing, digital microscopy, X-ray analysis, and solderability testing. Using advanced equipment like Leica digital microscopes and X-ray systems, we confirm the visual conformity, internal consistency, and overall integrity of electronic components.
- Outbound shipment verification: Before shipment, every batch undergoes a final verification to ensure that it meets all specified quality standards. This step is crucial to prevent any discrepancies and ensure that only the highest quality components reach our customers.
2. Advanced Testing Techniques
We use various advanced testing techniques to uphold our quality standards.
These include:
- Mechanical testing: Measuring components using physical and digital tools to verify their dimensions.
- Digital microscopy: High-powered analysis to confirm visual conformity to manufacturer specifications.
- X-ray analysis: Inspecting internal structures to detect any hidden defects.
- Acid decapsulation: Exposing internal die and wire bonds for detailed examination.
- LCR testing: Verifying inductance, capacitance, and resistance of passive components.
- Solderability testing: Ensuring proper solder wetting performance to prevent assembly issues.
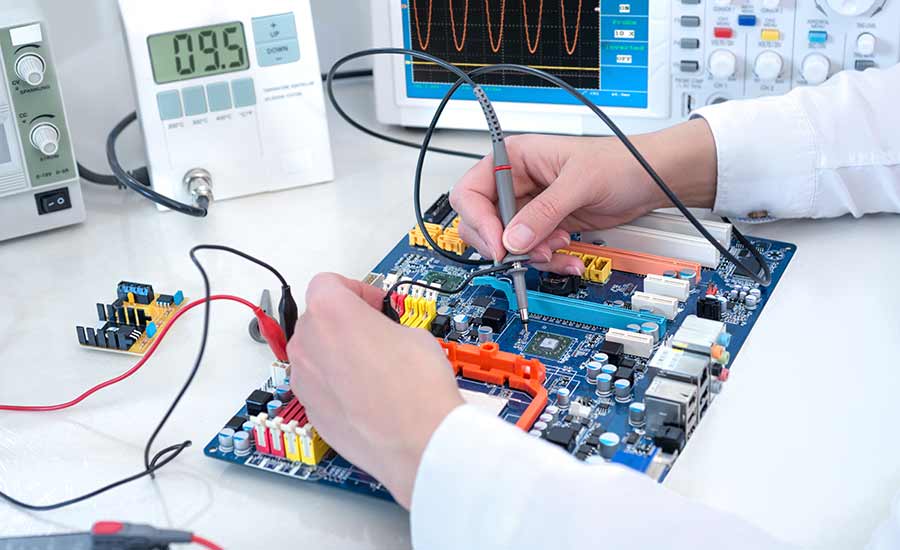
AGS Devices: A Reliable Partner for Quality Control
At AGS Devices, we bring nearly 20 years of expertise in the electronics sector, specializing in top-tier quality control for electronic components.
Our mission is to supply and distribute top-quality integrated circuits, resistors, capacitors, transistors, and diodes — key components that power and advance technologies.
As a leading distributor of electronic components, we are dedicated to enhancing the efficiency and reliability of your supply chain through rigorous quality control measures.
Our experienced team utilizes the latest technology and insights to deliver high-quality components at competitive prices, ensuring that every product meets the stringent demands of modern AI applications.
In addition to quality control services, we also provide a wide range of electronic components, including:
- Power Supply Distributors
- Optoelectronics
- Circuit Protection
- Interconnects
- Passive Components Electronics
- Electronic Testing Equipment
- Electromechanical Devices
Our meticulous approach to quality control guarantees that every component we supply enhances the performance and reliability of your projects.