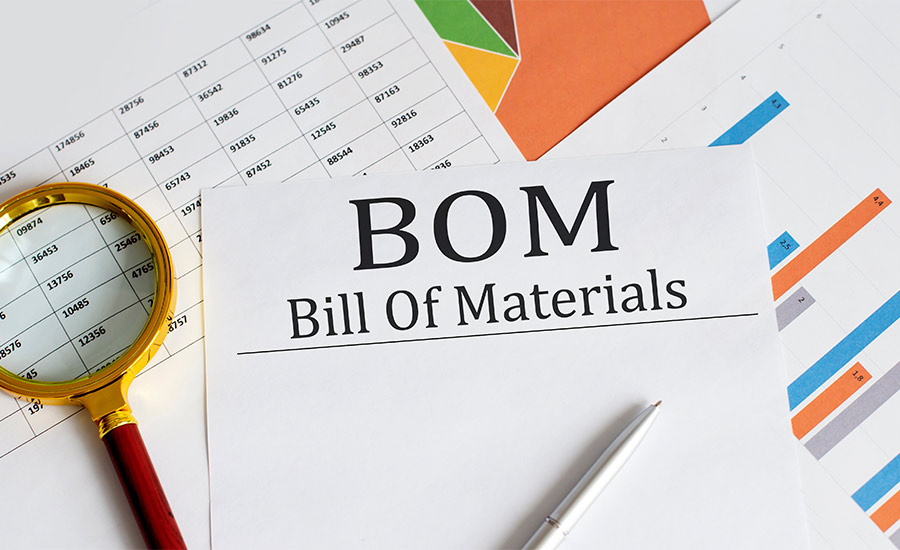
Bills of materials (BOM) are an important component of product development, manufacturing, and supply chain management.
According to a recent study by the Aberdeen Group, companies with effective BOM management processes are 50% more likely to launch products on time and 55% more likely to deliver those products to customers as promised.
We’ll cover the basics of a bill of materials, explore different types of BOMs, and show you how to create a bill of materials with the help of AGS Devices.
What Is a Bill of Materials (BOM)?
A bill of materials (BOM) is a source of information that lists every component, part and raw material required to build your product. It lists a finished product at the top of the document with all other components listed below.
The core benefit of a BOMs is that it’s a useful tool that guides the production process, helps track inventory, and improves communication between your team and suppliers.
In the manufacturing industry, where there are many engineers, purchasing managers, and supply chain professionals, a BOM keeps everyone on the same page for effective operations.
Types of Bills of Materials
The two main types of bills of materials are the engineering BOM and manufacturing BOM. Sales BOMs, service BOMs, and single vs. multi-level BOMs are also considered BOM types, but for more specialized or niche roles.
Let’s see what each type of BOM has to offer:
1. Engineering BOM (EBOM)
The Engineering BOM (EBOM) is created during the product design stage.
It includes data of all the parts and assemblies defined by the engineering team, demonstrating how the product should be built based on its design.
The EBOM provides a clear picture of the product’s structure by listing all components, subassemblies and technical details.
It acts as a blueprint for engineers and designers, helping them collaborate with manufacturing teams to start production.
2. Manufacturing BOM (MBOM)
While the EBOM focuses on design, the Manufacturing BOM (MBOM) is all about the production phase.
MBOMs include information about every part, material, and subassembly needed for manufacturing, along with product assembly instructions.
The MBOM also considers packaging materials, labels, and other items required for product completion.
If your team works with external suppliers or contract manufacturers, the MBOM provides the clear, detailed information they need for production according to your specifications.
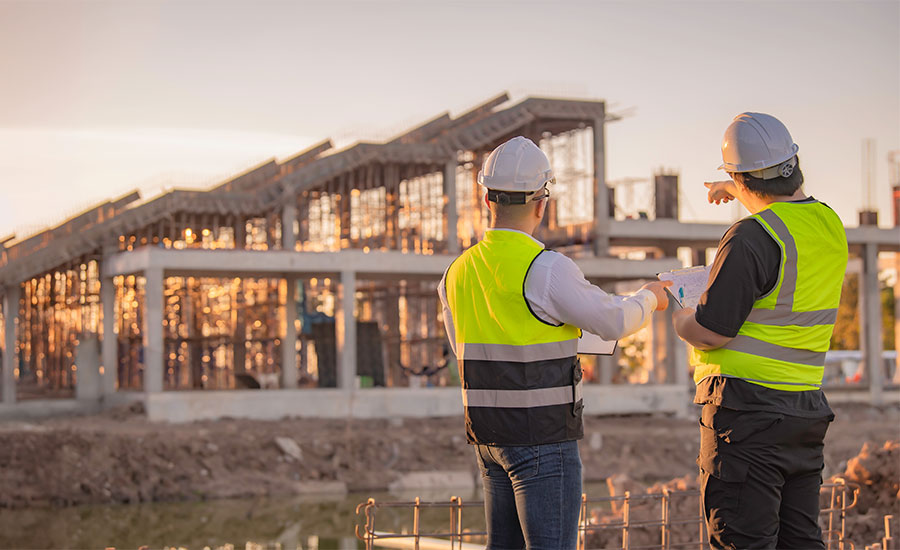
3. Sales and Service BOMs
Sales and service BOMs are useful when you need to interact with customers or provide after-sales support.
The sales BOM outlines product components that can be sold as separate items, giving the sales team a breakdown of what’s included in the final product.
The service BOM, on the other hand, focuses on maintenance and repairs as it lists the components and instructions needed for product servicing, which help service technicians efficiently diagnose issues and replace faulty parts.
4. Single vs. Multi-Level BOMs
A single-level BOM provides a straightforward list of all components and materials needed for a product — useful for simple products without many subassemblies.
While it’s easy to read, it lacks the information needed for complex products.
In comparison, a multi-level BOM breaks down the product into a hierarchical structure of individual parts and subassemblies.
It accommodates greater detail and is essential for complex products where certain assemblies comprise multiple components. With a multi-level BOM, you get a bird’s eye view of how everything connects, simplifying inventory, production, and servicing management.
Components of Bill of Materials
Being familiar with a BOMs’ essential components and bill of materials examples will help you create a roadmap for production, inventory management, and procurement.
These are the core components of a BOM:
Part Numbers and Descriptions
Part numbers are unique codes that identify each component in your BOM.
They help you and your team quickly find and reference parts during ordering, inventory checks, or repairs.
Descriptions also add valuable details about each part, making it easy to distinguish between similar parts.
For example, instead of listing “screw,” you might write “2-inch stainless steel screw,” which gives a clearer description of the item and helps avoid mistakes when ordering or using the part.
Quantities and Units of Measure
Quantities tell you how many of each part you need to make one product.
This component is important so you can order the correct amount from suppliers and properly plan your production process.
You also need to include the unit of measure, like “each,” “meters,” or “lbs” to ensure everyone knows exactly how much of each part to get.
Being specific with units of measure helps keep things consistent, especially when parts come in different sizes or forms.
For example, if you’re building a chair, you might need four screws (each) and two meters of wood. This clarifies what exactly you need to order.
BOM Levels and Hierarchies
A BOM can have different levels, especially for more complicated products. These levels break the product down into smaller parts, like subassemblies, components, and raw materials.
Each level shows a different part of the assembly process. For example, in a simple table, the top level might represent the finished table, while the lower levels would show the parts needed, like the legs, tabletop, and screws.
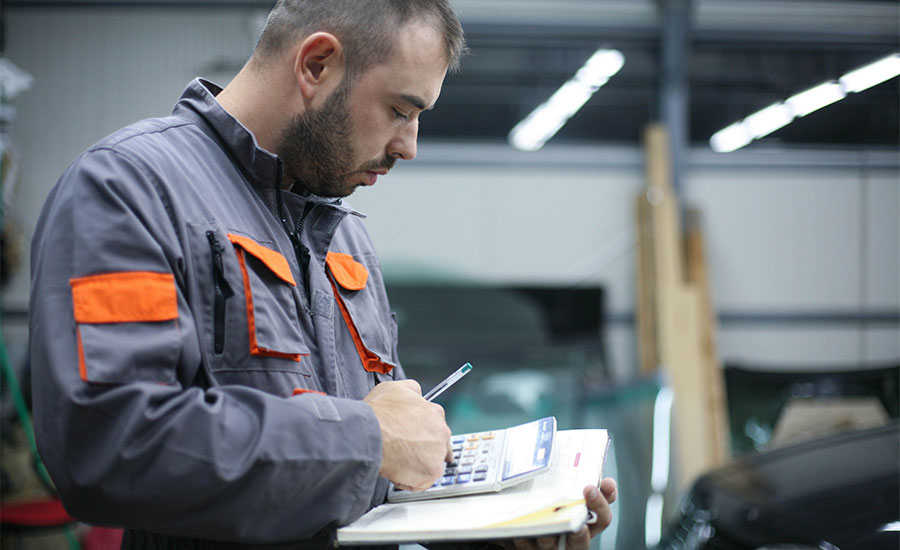
How To Create a Bill of Materials
A well-structured BOM improves communication between teams, prevents costly production delays, and keeps everyone aligned on what’s needed.
Here’s a step-by-step guide to help you build a BOM that works:
1. Gather Detailed Product Information
Start by listing everything you need to make your product. This includes all the parts, materials, and any smaller assemblies that go into the final product.
For example, if you’re building a table, your list might include items like legs, tabletop, screws and wood glue.
2. Assign Unique Part Numbers
Give each part a unique code or number so you can easily identify it.
For example, you could label the screws as “SCR001” and the table legs as “LEG001” for better organization and an improved ordering process.
3. Create Clear Descriptions
Write a short description for each part to make sure everyone knows exactly what it is.
For example, instead of just writing “wire,” you could describe it as “10-gauge copper wire, 3 meters.”
4. Define Quantities and Units of Measure
Specify how many parts you need and in what unit.
For example, for the table, you might need four legs (pieces) and one liter of wood glue. This helps ensure you order the right amounts and avoid running short during production.
5. Organize Components Into BOM Levels
For more complex products, break things down into levels.
The top level is the finished product (the table), and lower levels show the parts and subassemblies (like legs, screws, and tabletop).
6. Add Notes and Attachments
If there’s anything special to note about a part, add it here.
For example, you might attach a drawing that shows exactly where the screws go or a note about using a specific wood type for the tabletop.
7. Use BOM Software for Easy Management
While you can use a spreadsheet to create a BOM, using specialized software makes it easier.
Tools like PLM (Product Lifecycle Management) software allow you to manage changes, collaborate with your team, and keep everything updated in one place.
Learn More About BOM Management With AGS Devices
At AGS Devices, we understand how important efficient BOM management is for keeping your projects on track. With our broad industry expertise, we ensure your BOM files are processed, scrubbed, and returned quickly, helping you avoid delays.
By uploading your BOM to our platform, we validate and verify parts of our in-stock inventory, giving you a fast and accurate quote. We also stay ahead of supply chain disruptions by planning for shortages and extended lead times, ensuring your parts are available when you need them.
Besides valuable support in streamlining BOM Management, we also provide services such as:
Our dedicated account representatives and sales managers work closely with you to find alternative solutions for any cost or supply challenges. We keep communication lines open, ensuring you’re always the first to know about any changes affecting your supply chain.
Start streamlining your BOM management today with AGS Devices and get your project moving in the right direction.
CTA: Ready to improve your BOM management? Upload your BOM today.