Semiconductor Shortage: Key Points
- The global chip shortage was triggered by several reasons, such as supply chain disruptions, surging demand, and geopolitical factors
- Industries like automotive, consumer electronics, and defense experienced significant delays and revenue losses
- Major risks include over-reliance on specific regions, limited foundry capacity, and lack of real-time visibility across the supply chain
- Solutions include diversifying supplier bases, reshoring manufacturing, and adopting smarter inventory management systems
The shortage of semiconductors not only slowed down the tech industry, but it also had an impact on nearly every sector, ranging from automotive to aerospace.
At the height of the crisis, automakers lost an estimated $210 billion in revenue in 2021 alone. While the production of new cars saw the most visible impact, every industry that relies on microchips felt the pressure.
This blog breaks down:
- What caused the global semiconductor shortage
- How supply chain vulnerabilities impact critical industries
- The biggest risks facing semiconductor procurement today
- Smart strategies to navigate and reduce disruptions
Semiconductor Shortage Causes & Outcomes
The global semiconductor shortage didn’t stem from one single cause — it was the result of several compounding factors that exposed just how vulnerable the supply chain really is.
From unexpected global events to structural inefficiencies, here’s how it unfolded:
1. COVID-19 Disruptions and Demand Surge
The pandemic created the perfect conditions for an increased semiconductor demand.
- Factory slowdowns in Asia and Europe left wafer production and chip packaging stalled just as the world was going digital overnight.
- Meanwhile, remote work and learning skyrocketed demand for laptop, webcam, router, gaming console, and server demands — all of which need advanced chips.
- Semiconductor demand spiked by more than 17% in recent years, outpacing the industry’s ability to recover.
Result: Massive lead time increases, strained fabrication capacity, and backlog across industries — from smartphones to cars.
2. Geopolitical Tensions and Trade Barriers
Tensions between the U.S. and China, along with export controls and sanctions across, disrupted relationships between key semiconductor companies and suppliers.
- The U.S.-China trade war introduced export restrictions, blacklisting companies like Huawei and SMIC, which in turn stockpiled chips and tightened supplier relationships.
- China accelerated its chip independence strategy, increasing demand for local foundry equipment and materials.
- Taiwan’s TSMC, which produces ~60% of the world’s semiconductors, became a focal point of global tech competition.
Result: International cooperation slowed and supply chain agility vanished. Companies scrambled to rethink sourcing strategies.
3. Natural Disasters and Factory Downtime
Unforeseen events like the fire at the Renesas factory in Japan (a key automotive chip supplier) and the Texas power grid failure in 2021 halted production at major fabrication facilities.
- Given the specialized nature of chip manufacturing, even short disruptions caused ripple effects across the supply chain.
- These events didn’t just reveal fragility — they showed how interconnected and concentrated the semiconductor industry is.
Result: Even brief disruptions created ripple effects. When a single fab goes offline, it can take weeks to months to restart, causing shortages across multiple industries.
4. Supply Chain Concentration
- Over 75% of chip production happens in East Asia, with Taiwan, South Korea, and China as the epicenters.
- This geographic concentration makes the entire semiconductor ecosystem extremely sensitive to regional disruptions, political instability, or resource constraints.
Result: A single point of failure — like a policy change or supply chain bottleneck in one country — can stall global output.
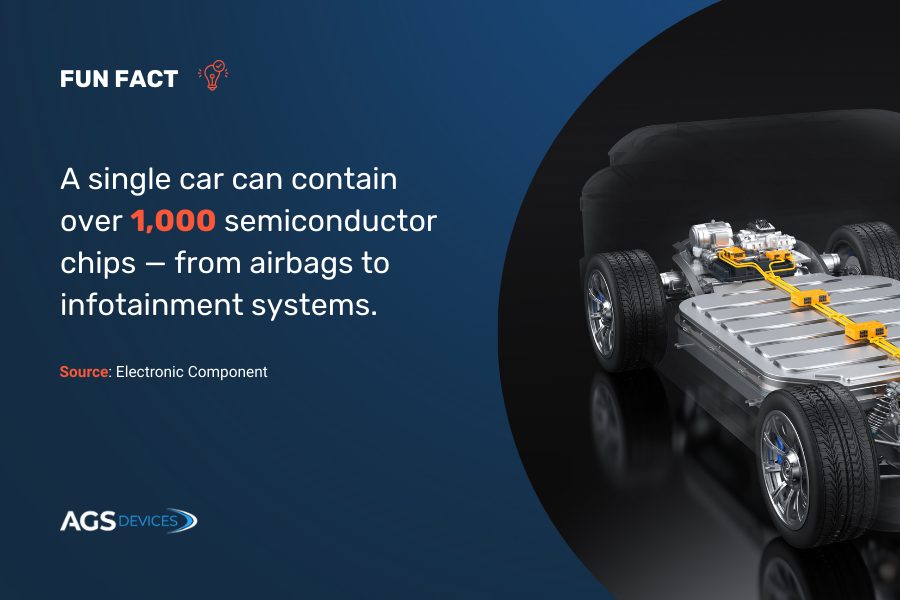
The Impact of Supply Chain Challenges on Key Industries
Critical industries were severely impacted by the semiconductor shortage, highlighting the modern world’s reliance on microchips.
Here are the industries that were affected the most.
1. Automotive Industry
Modern vehicles are increasingly reliant on semiconductor chips to power a wide array of systems, from basic engine controls to advanced driver-assistance features.
During the height of the shortage, automakers like Ford, GM, and Toyota were forced to cut production, leave out high-tech features, or halt entire product lines — leading to billions in lost revenue.
2. Consumer Electronics
Smartphones, laptops, gaming consoles, and smart home devices all rely on advanced semiconductors.
Companies like Apple and Samsung experienced delays in manufacturing, with consumers waiting longer for new product releases or restocks.
The shortage also raised the cost of components, squeezing margins for smaller electronics manufacturers.
3. Industrial and Manufacturing Sectors
Semiconductor shortages slowed the rollout of automation systems, IoT devices, and factory controls. This limited industrial innovation and increased downtime for companies trying to modernize operations in a post-pandemic world.
4. Healthcare and Medical Devices
Essential equipment like ventilators, diagnostic tools, and portable monitors depend on specialized chips.
Any delay in sourcing semiconductors affected the availability and production of these critical devices, particularly during COVID-19 surges when demand peaked
The shortage of semiconductors has demonstrated that silicon now powers every industry, from mobility and consumer tech to critical infrastructure.
Key Supply Chain Risks in the Semiconductor Ecosystem
Making semiconductors is already hard. Keeping the supply chain moving smoothly? Even harder.
Here are the biggest vulnerabilities still facing the industry today:
- Geographic bottlenecks: Over 60% of advanced chips are made in Taiwan. A single natural disaster or political event could disrupt global supply overnight.
- Limited foundry options: Fewer than five companies globally manufacture most of the high-performance chips. This heavy reliance on just a few fabs increases the risk of bottlenecks when demand spikes.
- Critical raw material dependencies: Semiconductors rely on neon gas (mostly from Ukraine), rare earths (primarily from China), and ultrapure silicon wafers. Any disruption here impacts the entire production line.
- Fragile logistics chains: Remember the Suez Canal blockage? That event alone delayed millions of dollars’ worth of chip shipments, proving just how vulnerable global trade routes are to disruption.
- Lack of visibility in tier-2 and tier-3 suppliers: Many OEMs don’t have a clear picture of who’s supplying their suppliers. This makes it hard to predict where the next disruption will come from.
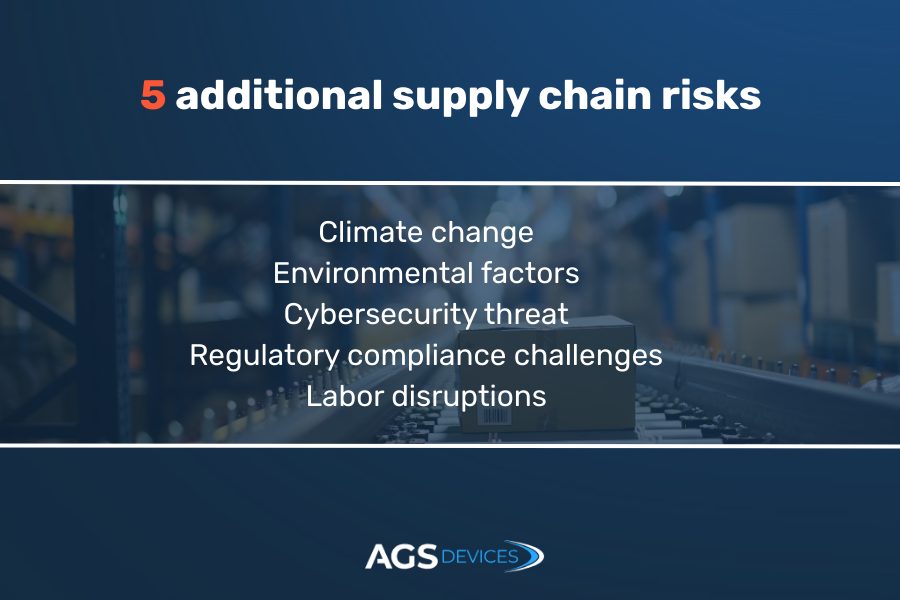
Strategies for Managing Semiconductor Supply Chain Disruptions
Navigating global chip shortages requires more than just quick fixes. Forward-thinking companies are reimagining how they source, manage, and forecast semiconductor supply to stay resilient.
1. Diversify Supplier Networks
Relying on a single region or supplier is a high-stakes gamble. Leading manufacturers are:
- Expanding their supplier base across North America, Europe, and Southeast Asia.
- Partnering with authorized distributors and specialized sourcing teams to track down hard-to-find components.
- Developing multi-vendor strategies to build redundancy into their supply chains.
Example: Automotive companies like Ford and General Motors have begun working directly with chipmakers to bypass bottlenecks and secure dedicated chip allocations.
2. Invest in Localized Manufacturing and Foundries
Geopolitical risks and transport delays have spotlighted the need for onshore and nearshore capacity.
- The U.S. CHIPS Act is injecting $52 billion to boost domestic semiconductor manufacturing.
- Companies are building fabs closer to end-use markets, reducing reliance on overseas supply chains.
Case in point: Intel is building new fabs in Ohio, while TSMC is investing in U.S. and Japanese facilities to diversify production.
3. Leverage Forecasting and Inventory Management Tools
Predictive tools are becoming essential for staying ahead of demand spikes and disruptions.
- Advanced analytics platforms can model component lifecycles, lead times, and demand shifts in real time.
- Buffer stock strategies — combined with smarter inventory categorization — are helping OEMs avoid shortages without overstocking.
Insight: Companies using AI-based demand forecasting saw up to 20% improvement in inventory accuracy during the height of the chip shortage.
Semiconductor Crisis: Key Takeaways
- Supply chain resilience is now a strategic priority. Companies must go beyond cost-saving to ensure reliability and agility.
- Localized manufacturing is gaining traction. Countries and companies are investing in regional fabs to reduce overseas dependency.
- Visibility matters more than ever. Forecasting tools, inventory transparency, and agile sourcing strategies are key to staying ahead.
- Collaboration is crucial. Building strong relationships with reliable sourcing partners like AGS Devices helps navigate both current shortages and future disruptions.
How AGS Devices Supports Clients During Semiconductor Shortages
At AGS Devices, we understand the pressure global shortages place on your operations — from delayed production timelines to budget overruns and missed market opportunities.
That’s why our sourcing experts specialize in hard-to-find, obsolete, and time-critical components.
Here’s how we help our clients stay ahead:
- Global sourcing network: We tap into a diverse, vetted network of suppliers across the U.S., Europe, and Asia to locate critical components — fast.
- Shortage & obsolescence solutions: From last time buys to lifecycle forecasting, our team helps you avoid costly redesigns and delays.
- Certified quality assurance: All components go through rigorous testing and inspection processes in line with ISO 9001, AS9120, and IDEA-STD-1010-B standards.
- Real-time communication: You’ll always know your order status, lead times, and available alternatives — no guesswork, just transparency.
- Personalized BOM support: We help manage, optimize, and fulfill your BOM management with precision, even under high-pressure conditions.
Whether you need a reliable buffer for your automotive designs, continuity for aerospace builds, or support during a product ramp-up — AGS Devices is here to keep your supply chain resilient.