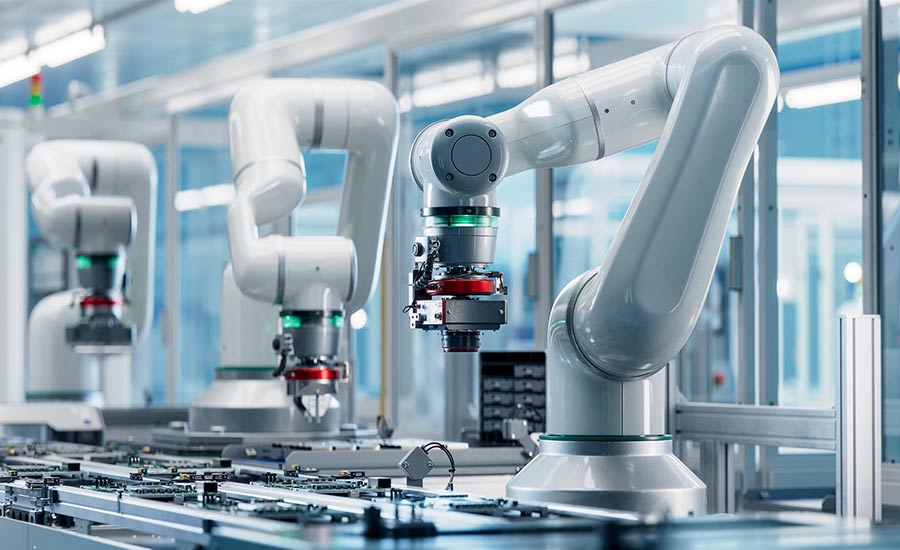
Think smartphones, medical devices or self-driving cars: They improve our lives in various ways, and behind every example lies a complex manufacturing process.
Global demand for electronics is expected to reach $1.3 trillion by 2028, and product manufacturing speed is expected to increase accordingly.
Because of this growth, manufacturers need to tackle important issues such as supply chain disruptions, quality control implementation and technological advancements.
So, how do you keep up?
In this blog, we’re going to go over the basics of the electronics manufacturing process, list common challenges that occur on a daily basis, and go over useful strategies you can use in manufacturing.
Understanding the Electronics Manufacturing Process
Every manufacturing process needs to have a starting concept and a list of sourcing components for your product.
Without a starting blueprint and building blocks, you can’t have a product..
Once you have a starting concept that’s ready to be realized, you can move forward.
Let’s see what comes after that:
1. Assembly
In this process, raw materials and electronic components become one.
This includes:
- Surface mount technology (SMT): This process includes attaching tiny components onto a circuit board with incredible precision.
- Wave soldering: All circuit boards are passed through a wave of molten solder.
2. Quality Assurance
Once the products are created, they need testing. Quality assurance requires rigorous testing because, in this process, you are delivering trust and security to your clients.
Two important QA tests are:
- Functional testing: Is the device working without issues and can it be turned on/off?
- Environmental testing: Can the product handle extreme conditions such as heat, cold or vibrations?
3. Packaging and Distribution
After quality testing, the finished product is packaged to prevent any type of damage and sent to consumers around the world.
Picture rows of smartphones, wrapped and ready to ship, destined to power someone’s daily life.
Common Challenges in Electronics Manufacturing
This industry faces numerous challenges that can affect production and innovation.
Common challenges in manufacturing are:
1. Component Shortages
If there’s a global shortage or logistical issues in production, efficient supply chain management and alternative sourcing options can solve this challenge.
During the global chip shortage, manufacturers like Tesla were able to adapt by using alternative components such as microcontrollers and semiconductors to maintain production deadlines, showing how important flexibility and foresight are.
2. Quality Control in Global Supply Chains
Quality control in manufacturing is essential because it minimizes the risk of defective components that can cause a whole series of products to fail. Following quality control standards and rigorous testing is something every company needs to do if they want to keep their products alive.
Imagine healthcare industry product manufacturers didn’t test devices like pacemakers or medical diagnostic tools. A single defective component could have life-threatening consequences for patients who use them.
3. Assembly Complexities in High-Precision Manufacturing
If you have an advanced assembly process, it enables your company to reduce errors and improve in efficiently manufacturing electronics.
Companies that manufacture micro-sized components especially benefit from having fewer assembly complexities because even the smallest mistake would require additional work.
Apple uses SMT technology systems to ensure assembly process precision as it involves placing hundreds of microscopic components onto a single circuit board.
4. Technological Changes
By following emerging technologies, you can adapt quickly to market demands and integrate new innovations in your manufacturing process.
For example, the rise of AI and IoT technologies has forced manufacturers to develop their supply chains and adopt specialized ICs for advanced capabilities, ensuring their products remain competitive in a fast-evolving market.
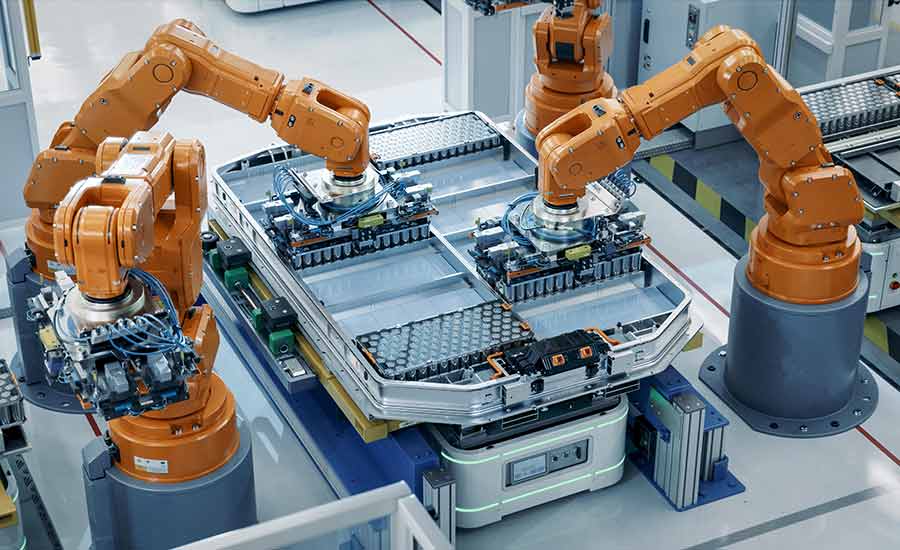
Strategies to Address Electronics Manufacturing Challenges
If you improve sourcing, leverage technology, and prioritize quality, you can navigate manufacturing complexities with ease and stay competitive.
Strategies you should use to address manufacturing challenges include:
1. Improve Supplier Networks for Reliable Sourcing
If you have a diverse supplier network in manufacturing, you’re most likely mitigating component delays and shortages.
With reliable supplier relationship management, you can consistently produce high-quality components, even when the manufacturing giants experience production struggles.
During the global chip shortage, many tech companies struggled with manufacturing, while Nintendo managed to use alternative suppliers to keep manufacturing their Switch consoles. This ensured that their fans could still get their hands on new gaming systems.
2. Use Technology for Automation
Technologies that use automation can reduce errors and improve efficiency in manufacturing.
Tools like AI-driven diagnostics and robotic assembly systems not only improve the speed of your manufacturing, but they also enhance precision.
For example, Intel uses automated SMT lines to manufacture high-performance motherboards and processors because SMT lines allow precise nanometer-scale components placement.
3. Ensure Quality Assurance Best Practices
Quality control isn’t just a step — it’s a continuous process that provides reliability and builds customer trust. It’s a continuous process that provides product security to your clients and builds relationships.
You’re not just providing safety to your clients; you’re giving them a guarantee that their product will have no issues or defects.
For example, companies like Boeing in the aerospace industry use X-ray inspections and stress tests to ensure flight control systems follow rigorous safety standards.
4. Mitigate Risks With Proactive Supply Chain Management
One of the ways you can avoid manufacturing risks is managing them before they escalate.
With a proactive supply chain management approach, you can forecast demands, plan for shortages and maintain inventories effectively to avoid delays.
During the COVID-19 pandemic, many companies went bankrupt, but there were also companies who used a proactively managed their supply chains. For example, ventilator and patient monitor manufacturers managed to predict the demand surges while stockpiling key components.
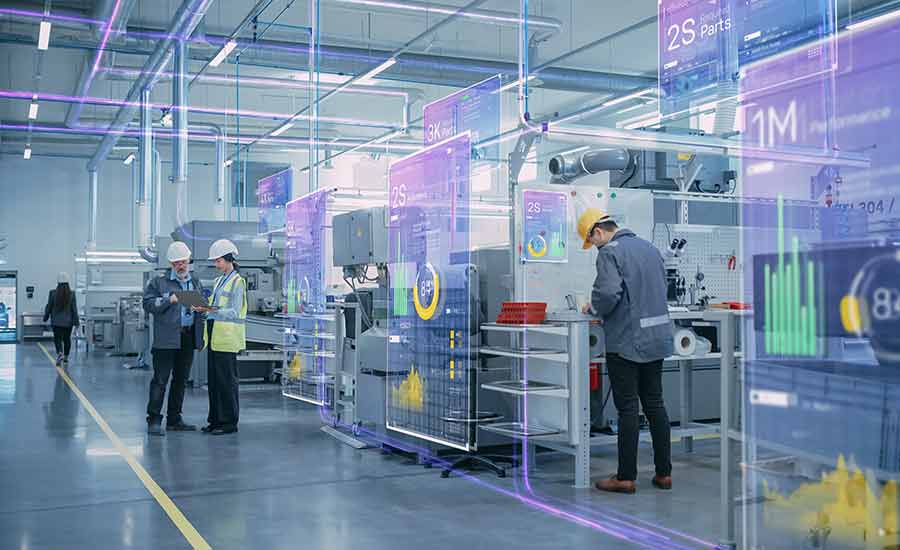
Future Trends in the Electronics Industry
Key trends that shape electronics manufacturing are worth mentioning because of changing market demands.
Future trends in this industry include:
- Technology miniaturization: Every piece of technology is becoming smaller, more powerful and it can contain more data. A perfect example of how miniaturization is used in devices is the Apple Watch. Who would have thought a few decades ago that we would have watches that monitor our heart rate, provide GPS instructions and calculate blood oxygen levels?
- AI and robotics automation: Robotics and AI-driven systems are streamlining production lines, reducing errors, and boosting efficiency. Tesla’s Gigafactories use AI-powered robotics for battery and EV manufacturing, enabling precision assembly at lightning speed.
- Using sustainable practices: Using recyclable materials and reducing energy consumption are becoming a standard in pretty much every industry, and the electronic components industry isn’t an exception. Samsung currently manufactures “green chips” using eco-friendly practices that align with global sustainability goals.
- 5G connectivity: 5G technology and infrastructure drive the need for advanced semiconductors because they are crucial for internet connections. Smart home devices like Amazon Echo rely on IoT-enabled ICs to connect and communicate with other devices.
How AGS Devices Simplifies Electronics Manufacturing Challenges
At AGS Devices, we are always proactive in exploring potential issues and trends in the electronics manufacturing industry.
If you’re experiencing issues with sourcing hard-to-find components or managing supply chain disruptions, we know how tackle those issues. Because of that, we’re here to provide customized solutions that help your processes and meet deadlines of your projects.
Our experienced team utilizes the latest technology and insights to deliver high-quality components at competitive prices.
We also distribute electronic components such as:
- Power Supply Distributors
- Optoelectronics
- Circuit Protection
- Interconnects
- Passive Components Electronics
- Electronic Testing Equipment
- Electromechanical Devices
We’re not just a supplier; we’re your partner in overcoming challenges. Whether it’s sourcing high-quality ICs, addressing lead times, or adapting to rapid technological changes, AGS Devices is committed to supporting your success every step of the way.