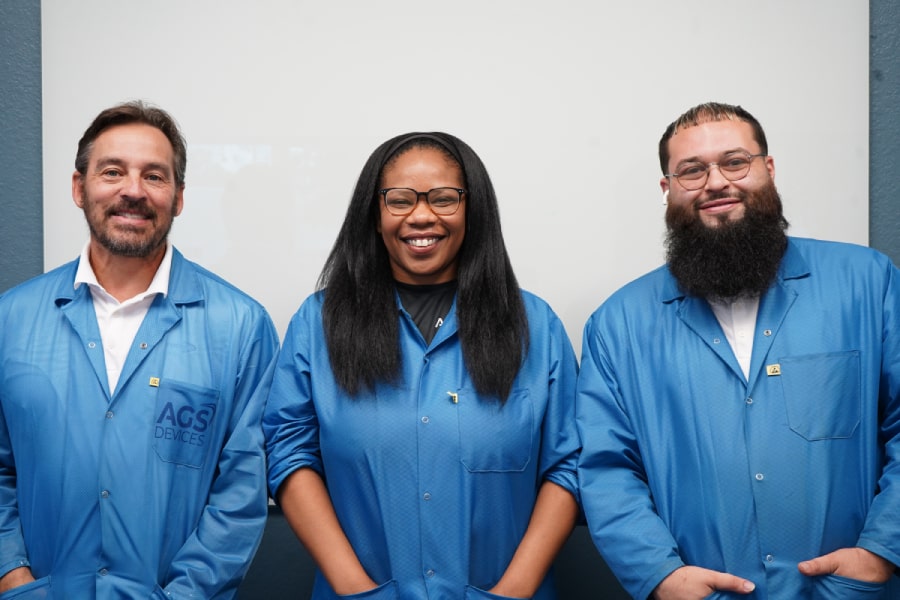
Quality control is more than just a checklist of boxes to tick in the electronic components industry — it’s a guarantee against fake parts and testament to trustworthiness.
Quality is important to us at AGS Devices, and we go above and beyond with our quality control procedures to make sure each product lives up to our high standards.
This interview will detail our team’s experience, technologies, and quality control procedures.
An Overview of the Quality Control Process
Q1: Could you briefly describe AGS Devices’ quality control procedure and its significance to the electronic components sector?
Quality control at AGS Devices starts as soon as materials are delivered to our location following a thorough, multi-step inspection procedure.
We follow internationally accepted standards, like IDEA-STD-1010B, which describes the requirements for accepting electronic components on the open market.
This quality control procedure is essential to ensure the parts we provide are brand new, never used, and handled in compliance with industry standards.
Three main steps comprise our process: outgoing processing, thorough quality inspection, and arriving inspection.
This comprehensive approach is essential given the high likelihood of counterfeit parts in the market. By adhering to strict processes, we ensure that every component meets the reliability and performance standards our clients expect.
Key Standards: J-STD-002D (Solderability Tests), IPC-A-610D (Acceptability of Electronic Assemblies), MIL-STD-1695 (Minimum Standards for Military Hardware), and IPC/JEDEC J-STD-033B.1 (Handling Moisture/Reflow Sensitive Surface Mount Devices) are the standards we refer to in addition to IDEA-STD-1010B. These manuals are a valuable tool for onboarding and retraining staff members, keeping our group updated on the most recent developments in the field.
Comprehensive Inspection Techniques
Q2: What methods and standards are applied to guarantee incoming electronic components fulfill quality requirements?
Stage 1: Initial Inspection Materials undergo a thorough incoming check upon arrival. As a first step, we verify quantities, part numbers, lot numbers, date codes, Certificates of Conformance, and test reports to ensure all documentation is compliant.
Since maintaining the integrity of the packaging is essential, we check shipping boxes, reels, tubes, trays, and bulk packing for damage. Moisture-sensitive components are checked to ensure the appropriate moisture barrier bags, desiccant, and indication cards are used, and items are also inspected for ESD-compliant packing.
The materials are then separated into groups by date code, lot number, manufacturer, and part number. For every batch, internal traceability records are created to guarantee meticulous tracking all throughout the process. Only when all compliance requirements are met can materials move on to the next phase — if not, they are segregated and reported for proper disposal.
Step 2: We do a comprehensive quality assessment based on several sources, including manufacturer datasheets, supporting paperwork, and internet databases like ERAI for high-risk counterfeit parts. In this phase, our highly skilled inspectors perform an in-depth audit, verifying the components against known authentic parts by examining their surface features, marks, and structural integrity using digital microscopy.
Step 3: Inspection of Outgoing Processing Components undergo a final review to ensure they satisfy all criteria and meet industry standards before being shipped to clients. This procedure guarantees our factory only produces compliant, high-quality items.
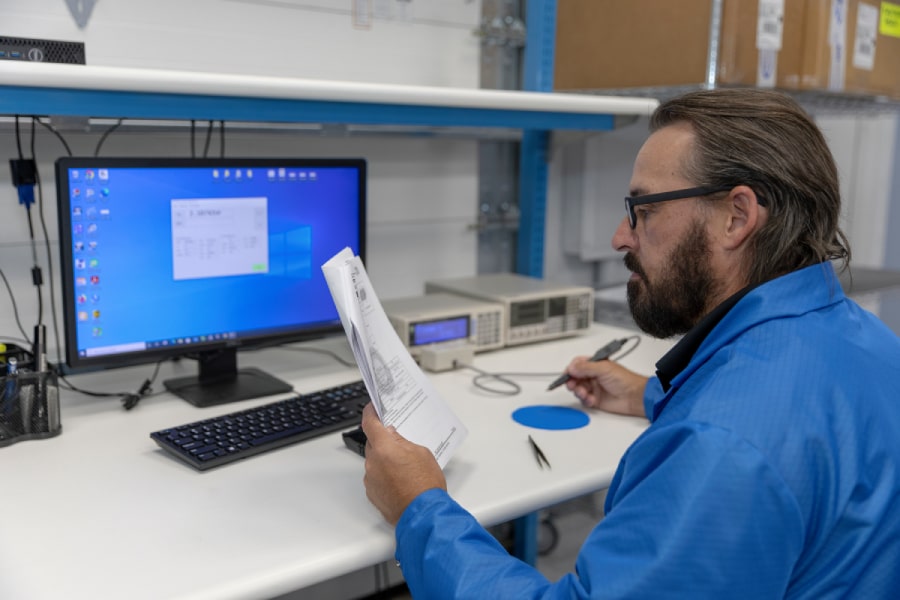
Utilizing Cutting-Edge Technologies
Q3: How does AGS Devices leverage cutting-edge technology like X-ray analysis and digital microscopy to guarantee component authenticity and compliance with industry standards?
AGS Devices uses cutting-edge technology in two ways:
1. Digital Microscopy
- High-resolution imaging: By capturing intricate images of electrical components, digital microscopes can identify surface flaws, shoddy marks, and anomalies. It takes a high degree of inspection to spot counterfeit goods.
- Non-destructive testing: One benefit of digital microscopy is its non-destructive method, meaning it can examine several samples in-depth without causing any damage.
- Documentation: To show we are adhering to standards, we include high-quality photographs in compliance reports and save them for future use.
2. X-Ray Examination
- Internal structure examination: A component’s internal construction, including wiring, die attachment, and bonding quality, is visible through X-ray imaging. This helps identify inferior or fake parts.
- Tampering detection: To ensure authenticity, X-rays can identify additional materials, hidden layers, or alterations.
- Verification of material composition: We confirm components are manufactured using the right materials under industry standards by examining the density and composition of the material.
- Integration: Our inspection processes incorporate these technologies. Our professionals get ongoing training, enabling them to correctly assess data and decide which components are legitimate.
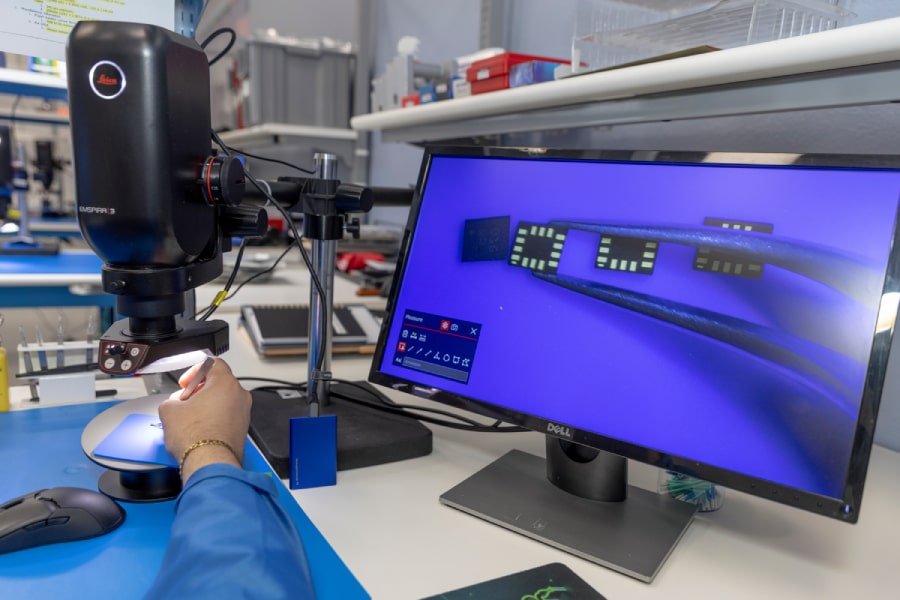
Procedures for Testing in Quality Assurance
Q4: Could you explain the procedures for establishing form, fit, and function specifications and the testing procedures used to guarantee the quality of electronic components?
AGS Devices uses a variety of testing techniques to confirm every part satisfies its form, fit, and function (FFF) requirements:
- Visual inspection: Using digital microscopes, components are first inspected for physical damage, erroneous marks, or inconsistent labeling. This process swiftly filters out obviously damaged or counterfeit parts.
- Digital microscopy: To ensure the component meets its specs, high-resolution digital microscopes are next utilized to inspect surface features including solder quality and physical measurements.
- X-ray analysis: To ensure the interior structure meets quality standards, X-rays offer non-destructive means of inspecting internal features, including die attachment and wire bonding.
- Electrical testing: Components are tested to ensure functionality, evaluating factors like voltage, current, resistance, and capacitance (by independent test houses, if necessary). By taking this step, you can be confident that every part operates within the permissible range.
- Environmental & stress testing: To assess a component’s resilience and dependability in harsh environments, we submit it to mechanical stress, humidity testing, and temperature cycling through third-party testing.
- Form, fit, and function (FFF) testing: To confirm components adhere to their design criteria, we check for proper operation within the intended system (function), mechanical compatibility (fit), and physical dimensions (form).
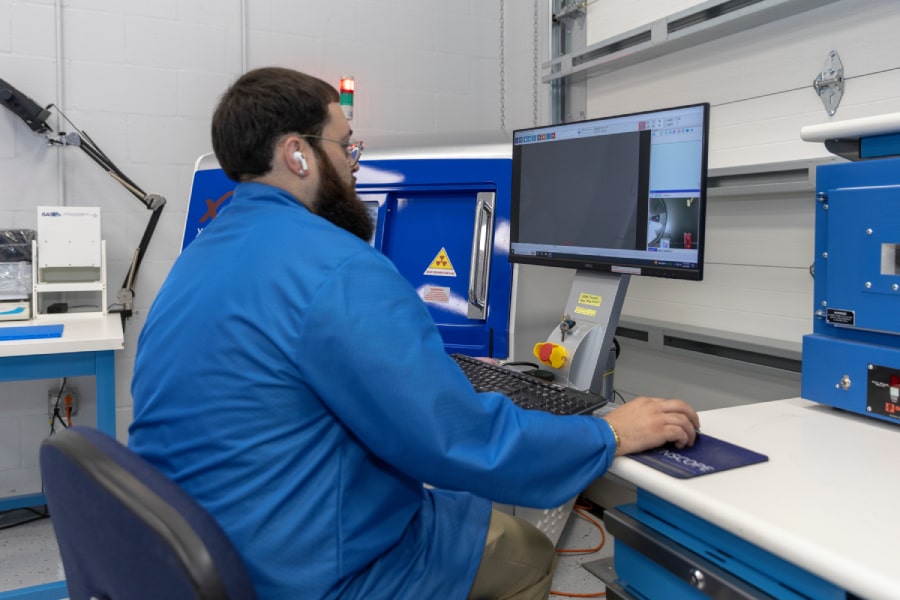
Protocols and Certifications
Q5: What accreditations and guidelines does AGS Devices follow to guarantee the quality of its goods and services?
When it comes to quality inspection and the authentication standards for electronic components, AGS Devices adheres closely to IDEA-STD-1010-B. We also use IPC-A-610D as a standard for measuring solderability. We can get parts directly from manufacturers for comparison thanks to internal protocols like “Gold Unit Purchasing,” improving the dependability of our testing procedures.
- Packaging integrity: To guard against damage during transit, we confirm the stability of the packaging. This covers material analysis for packing, drop testing, and visual inspections.
- How these standards help: By adhering to these international standards, we keep fake parts out of the supply chain and provide our clients with high-caliber goods.
Requirements and Day-to-Day Activities
Q6: Could you describe a typical day in the life of the AGS quality control team and what credentials and experience are needed for team members in the department?
It is essential to understand ISO 9001, IPC standards, and inspection methodologies. Crucial abilities include effective communication, problem-solving, and attention to detail.
A Typical Day at AGS Devices
The day starts with a team meeting to discuss objectives and tackle pressing issues. Inspectors then examine incoming materials and keep an eye on the production process.
Preparing compliance reports, recording findings, and reviewing inspection data are all part of midday work. The team troubleshoots quality concerns and works on projects related to continuous improvement in the afternoon.
The day ends with a wrap-up meeting to plan the next day, which often includes training on new methods.
Overcoming Supply Chain Difficulties
Q7: What are some of the main current issues that the supply chain for electronic components is facing, and how is AGS handling them?
The supply chain for electrical components must contend with issues like fake parts, shortages in supply, and hiccups in logistics. AGS uses proactive risk management techniques, solid supplier relationships, shortage and obsolescence solutions and strict quality control processes to address these problems.
Our rigorous inspection procedure guarantees only genuine parts are supplied, preserving the supply chain’s integrity.
A Synopsis of Our Quality Control in One Word
Q8: What word, and why, would you choose to best describe AGS’s quality control procedure?
Meticulous. This term perfectly captures the strict attention to detail that characterizes our quality assurance procedure.
Every stage is carried out precisely to guarantee the highest degree of dependability in our electronic components, from initial inspection to final tests.
Learn More About Quality Control With AGS Devices
At AGS Devices, we specialize in the distribution of electronic components, following the highest standards of quality control.
Our process involves a thorough initial inspection and rigorous testing to confirm both our products’ authenticity and performance. This careful process ensures the electronic components we supply are top quality and meet the diverse high-performance requirements of various applications.
We also distribute electronic components such as:
- Power Supply Distributors
- Semiconductors
- Optoelectronics
- Circuit Protection
- Interconnects
- Passive Components Electronics
- Electronic Testing Equipment
- Electromechanical Devices