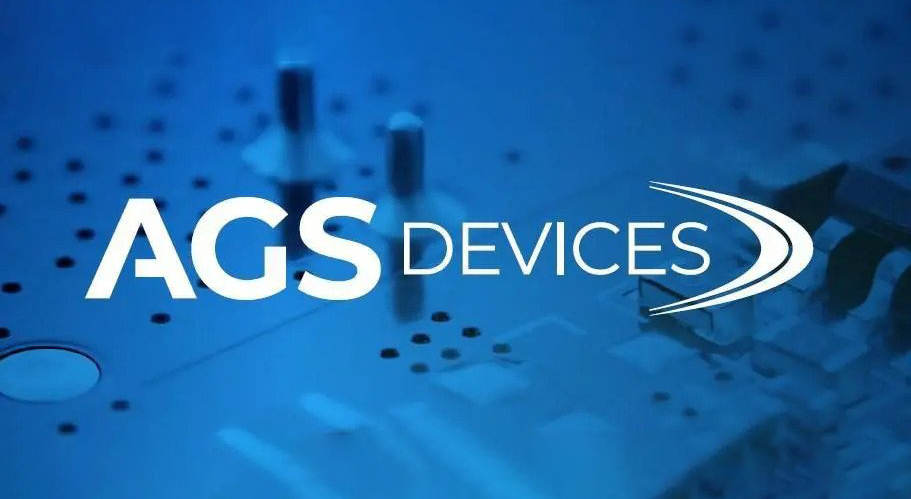
The global chip shortage that sent the automotive and consumer electronics industries reeling during the COVID-19 pandemic is, in many aspects, in the rearview mirror. However, industries around the world that have been grappling with electronic component shortages for nearly four years are still facing obstacles that may affect their businesses for years to come. Can the electronics industry overcome the challenges that lie ahead?
Global Pandemic Woes
In early 2020, the COVID-19 pandemic significantly impacted the electronics industry, disrupting supply chains around the globe, slowing down production and in many cases, bringing operations to a screeching halt. Pandemic-related factory shutdowns led to a massive reduction in the supply of electronic components. Additionally, many countries imposed lockdowns and travel restrictions, which further impeded the delivery of components and other goods.
The pandemic also led to a surge in demand for electronics as people found themselves working from home and spending more time on digital devices. This forced chip manufacturers to shift their focus to other areas, such as computer equipment and mobile devices, which spiked in demand with more people working remotely. As the need for 5G and cloud-based services exploded, more chips were needed for communication platforms such as Zoom and video streaming services. As a result, many tech companies faced difficulties in securing the components they needed to meet rapidly growing demand.
The shortage of electronic components also impacted the innovation and development of new technology. Companies struggled to secure the parts needed to create new products, hindering the growth of the tech industry. Additionally, the shortage led to a reduction in competition, as smaller companies were often unable to secure the components they needed to remain competitive.
During the pandemic, some companies hoarded supplies and bought more components than needed in case supply dried up. For example, companies like Huawei stockpiled supplies in advance of U.S. tech bans on China in 2021. These actions further exacerbated supply challenges.
Post-Pandemic Climate
Where do we stand now, as the immediate fears of the pandemic have largely abated? The Internet of Things, which has been on a sharp incline since before COVID-19, continuously pushes semiconductors ahead of oil as the world’s key commodity. The U.S. leads the world in developing and selling semiconductors, but manufacturing has definitively shifted to Asia. Taiwan and Korea produce chips at a near monopoly – these two countries account for over 80% of global processor chip production and 70% of memory chip output.
Global growth currently hinges upon their production and inflation upon their prices – shortages related to rapid upswings in demand become inflationary. Viewed through a longer lens, the region’s lead will continue to expand with the increasing technical and capital strength required for future semiconductor production, effectively preventing any change to the duopoly in at least the next five years.
Tensions between the U.S. and China continue to impact the global supply chain, prompting new government controls on sales of chips to China, the world’s largest semiconductor market.
There are other significant policy challenges as well, such as strengthening the U.S. semiconductor workforce by reforming America’s high-skilled immigration and STEM education systems and promoting free trade and access to global markets, according to the Semiconductor Industry Association’s 2023 report on the state of the industry.
The Semiconductor Industry Association (SIA) added a positive note, saying the long-term outlook for the semiconductor industry remains strong, despite the challenges.
In a push to bolster domestic semiconductor production overseas, the European Union has approved the EU’s Chips Act, with the goal of producing 20% of the world’s semiconductors by 2030, Bloomberg reported. New plants at sites in Europe have already been announced by chip makers including Intel and STMicroelectronics.
A significant share of new chip manufacturing capacity and R&D is expected to be located in the U.S., in large part to the CHIPS and Science Act of 2022. The CHIPS Act was enacted by the government to provide semiconductor research investments and manufacturing incentives to fortify America’s economy, national security and supply chains. The goal of the nearly $300 billion expenditure is to prevent U.S. industries from experiencing similar semiconductor supply chain disruption in the future.
Intel, Taiwan Semiconductor Manufacturing Company (TSMC), Texas Instruments and Samsung have all announced plans to build fabs in the U.S., but that doesn’t guarantee an end to the chip shortage. As America’s semiconductor environment expands in the years ahead, so too will its demand for workers with the skills, training and education needed in this highly innovative industry.
According to a new SIA/Oxford Economics study, the semiconductor industry is projected to grow by more than 115,000 jobs by 2030, with 67,000 jobs at risk of being unfulfilled. It is estimated that between now and 2030, more than 3.85 million tech roles will be created, and 1.4 million of those roles are at risk of being unfulfilled. For companies who are filling semiconductor roles, building a deeper talent pool is of critical importance.
Expanding the supply of skilled designers and other semiconductor professionals will require consistent effort for many years, quite possibly decades. This talent squeeze is unfortunately not unique to the semiconductor industry, and will have a ripple effect on the entire world of technology.
Supply chain challenges stymie even the most experienced manufacturers and workers. Businesses should be willing to try new ways to get components they need. That may mean working with different suppliers or agreeing to make more bulk purchases with a current one.
AGS Devices understands the importance of being a reliable supply chain partner and the urgency of on-time delivery. The dedicated, always accessible team at AGS is connected to a vast worldwide network of suppliers and OEMs, providing flexibility to clients’ supply chain. As a stocking distributor, AGS has access to allocation of immediate stock regardless of standard lead times. The meticulous Quality Control processes, from incoming inspection to digital microscopy, x-ray analysis, LCR testing, solderability and more, AGS follows globally recognized standards and utilizes additional protocols to ensure the highest quality is delivered every time.
Meeting your electronic component needs
Of all of the variables within the technology industry that play a role in this current shortage, there is another, more volatile aspect that makes forecasting even more difficult. The current geopolitical climate is keeping virtually every tech business on high alert. From the Russo-Ukrainian conflict, to inflation shockwaves, to the growing fear of confrontation between China and Taiwan, the electronics industry must adapt to these geopolitical concerns. The best course of action for businesses is to remain informed, vigilant and flexible.